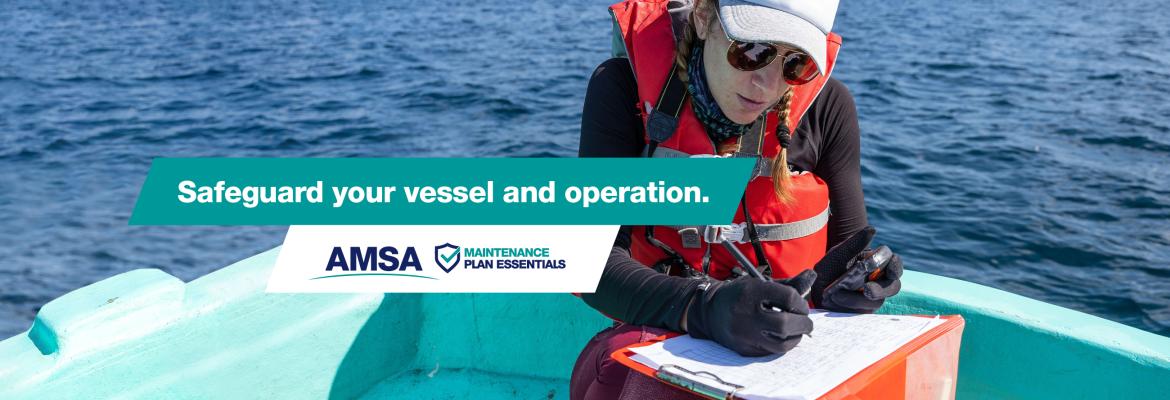
Undertaking simple, regular vessel and safety-equipment checks, and logging them while you do it, can help prevent small problems from becoming dangerous and expensive incidents. Under the National Law, it’s a legal requirement to have, and document, a regular programme of maintenance and inspection activities.
Maintenance plan essentials
Read on to discover:
- the benefits of having a maintenance plan
- why you need a maintenance plan
- what to include in your maintenance plan
- helpful maintenance plan tips and links.
What are the benefits of having a maintenance plan?
Having a maintenance plan helps you prevent dangerous and expensive incidents. Under the National Law, it’s a legal requirement to have, and document, a regular programme of maintenance and inspection activities.
Reduced maintenance costs
By outlining a preventive maintenance plan, small problems can be caught before they turn into big failures and costly repairs.
Extended asset life
Maintaining equipment and keeping it operating in good condition may extend its operational time, so it won’t need to be replaced as often which can help save you money.
Increased workplace safety
There is less chance of equipment failure which could harm someone or cause damage to other equipment.
Improved workplace culture
Involve your crew in developing and implementing a maintenance plan, as well as undertaking preventative maintenance tasks.
Decreases downtime
Unexpected machinery and equipment failures or accompanying crew injury can put your vessel out of operation, and you out of business.
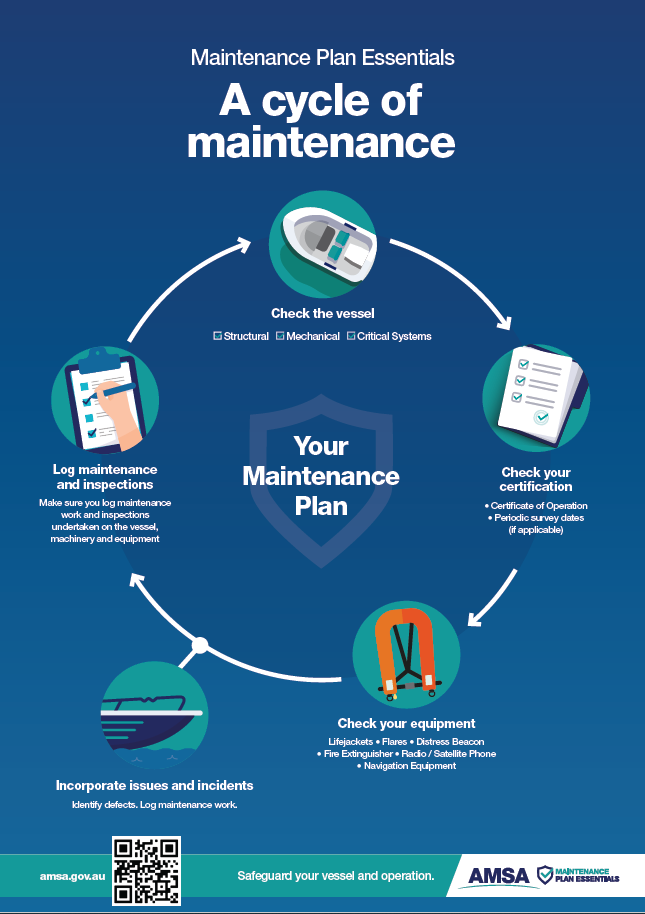
Why do I need a maintenance plan?
The regular checking and logging of vessel structure, critical systems, machinery and equipment, including safety equipment, is key to a safe, secure and legally compliant operation for owners, operators, crew and passengers alike.
DID YOU KNOW?
Recent incidents have demonstrated the potentially serious consequences a lack of effective maintenance poses to the safe operation of vessels.
- Analysis of 117 incident investigations since 2020 found maintenance problems were a factor in 28% of all incidents, including 50% of very serious incidents and 27% of serious incidents.
- Deficiencies relating to safety equipment (lifebuoys, lifejackets, first aid kits, flares, and firefighting equipment) were 5 of the top 10 most frequently identified deficiencies in domestic commercial vessels (DCVs) in 2020 and 2021.
There are also many DCVs with overdue periodic surveys. Another key element of a vessel’s maintenance plan is the management of its certification, and this includes ensuring that, where applicable, the vessel undergoes periodic surveys within the timeframes set out in Marine Order 503 – Certificates Of Survey – National Law.
Marine Order 504 requires that a vessel’s safety management system (SMS) include a system of regular programmed inspection and maintenance appropriate for the vessel, its machinery and equipment.
What should I include in my maintenance plan?
What you include in your maintenance plan will depend on your vessel. It’s important to take into account manufacturers’ recommendations and keep a record of your regular inspections and maintenance.
Safety equipment
Include regular checks of your safety equipment in your maintenance plan. For example:
- expiry dates for flares, emergency position indicating radio beacons (EPIRBs) and first aid kit items
- condition of lifebuoys including retro reflective tape and lights
- servicing dates for life-rafts, inflatable lifejackets, fire extinguishers and fixed firefighting systems.
Critical systems
Consider your critical systems on board including fuel, electrical, propulsion, steering, communication, navigation, bilge pumping arrangements, anchoring and sewage:
- consider the test date for residual current devices, and electrical insulation test
- regularly test bilge pumps and high-water alarms
- keep engine and machinery bays clean and dry - inspect regularly for early detection of fuel, hydraulic or oil leaks
- regularly check all hoses for chafe, cracking and leaking
- service your engines and other equipment in accordance with the manufacturer’s recommendations
- make regular test calls on your radios and other communications equipment
- check the health and terminals of your batteries
- check piping, vents, traps and gauges on sewage systems to avoid leaking of poisonous gasses.
Don’t wait until survey or inspection time to check these essential systems. You are responsible for ensuring your vessel meets the National Law requirements and is always safe.
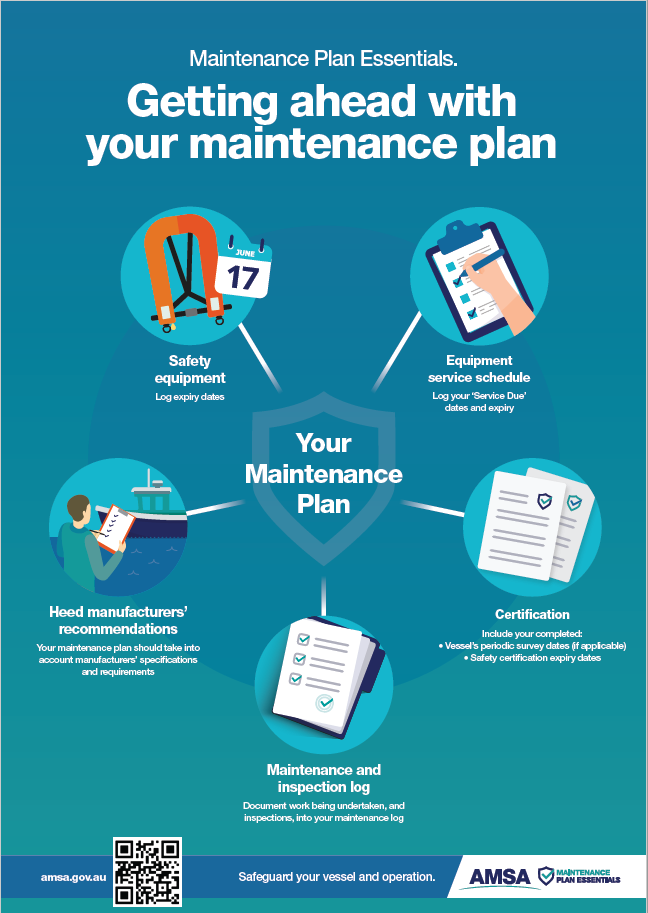
Maintenance plan tips
Defect identification
Inspections are key to your maintenance plan. Things break or wear out on boats constantly and having a system to quickly record the defect and follow up to make sure it is addressed is an important part of a maintenance plan. This could be part of your daily pre-start check.
Documentation
A lot of operators already have a good, planned maintenance system in place but fail to have a process to capture and record that maintenance.
AMSA has provided a template of a maintenance plan log sheet as an example of what you could use (Link).
Regular, smaller maintenance
Consider undertaking smaller pieces of maintenance more often, rather than trying to do everything at once. When documented, regular smaller maintenance activities can be reviewed to identify patterns, machinery, or systems with higher risks of failure, faulty or poor-quality parts etc.
Plan in advance
Safety equipment such as flares and first aid kits are not always readily available especially in more remote townships and operators need to order well in advance. Seasonal weather can also disrupt supply and availability of equipment and spare parts.
Need help with your documentation?
We've created some examples of the types of documentation you might use with your maintenance plan, including:
- a maintenance log PDF512.24 KB
- a maintenance checklist for small vessels PDF452.78 KB
- a certification record PDF516.58 KB.
Further information
Use the resources in this section to learn more about safety management and maintenance.
- Planned maintenance on domestic commercial vessels
- Guidelines for a safety management system
- Templates for a safety management system
- Marine order 504—Certificates of operation and operation requirements
- Lifejacket maintenance and storage
- Inspection of portable fire extinguishers PDF608.28 KB
- Correct use of hydrostatic release units
- NSCV section C7 - equipment guidance for certificate of survey vessels
- NSCV Part G - equipment guidance for non survey vessels